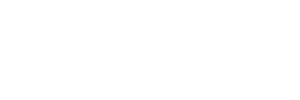
2023 Design-Build for Water/Wastewater
- Registration Closed
2023 Design-Build for Water/Wastewater
-
Includes Credits Recorded On: 03/16/2023
CONTENT EXPIRES: December 31, 2025 Progressive design-build was selected by Aqua Ohio for upgrades to the 10 MGD Ashtabula Water Treatment Plant - a new flocculation/sedimentation facility and filter improvements. Completing the project on time was mission-critical; essential to meet regulatory requirements of the Public Utilities Commission of Ohio and Ohio EPA. This project was a rate case project, meaning that recovery of the capital cost was only possible if it was constructed, commissioned, and treating water on schedule (by end of 2021). The Great Lakes Construction Co. HDR team was selected by Aqua Ohio with a notice to proceed issued in May 2020, leaving only 19 months for preliminary and detailed design, construction, commissioning, and acceptance. With careful planning, continuous communication, and effective collaboration, this tight schedule was achieved. Cutover to the new facilities and control system was seamless and accomplished in less than half the time allocated, indicating the quality of the designed and constructed project and engagement of Aqua Ohios Engineering and Operations throughout. At all times during the construction period, reliable delivery of high-quality water continued to Aqua Ohios customers.
CONTENT EXPIRES: December 31, 2025
Progressive design-build was selected by Aqua Ohio for upgrades to the 10 MGD Ashtabula Water Treatment Plant - a new flocculation/sedimentation facility and filter improvements. Completing the project on time was mission-critical; essential to meet regulatory requirements of the Public Utilities Commission of Ohio and Ohio EPA. This project was a rate case project, meaning that recovery of the capital cost was only possible if it was constructed, commissioned, and treating water on schedule (by end of 2021). The Great Lakes Construction Co. HDR team was selected by Aqua Ohio with a notice to proceed issued in May 2020, leaving only 19 months for preliminary and detailed design, construction, commissioning, and acceptance. With careful planning, continuous communication, and effective collaboration, this tight schedule was achieved. Cutover to the new facilities and control system was seamless and accomplished in less than half the time allocated, indicating the quality of the designed and constructed project and engagement of Aqua Ohios Engineering and Operations throughout. At all times during the construction period, reliable delivery of high-quality water continued to Aqua Ohios customers.
-
Includes Credits Recorded On: 03/16/2023
CONTENT EXPIRES: December 31, 2025 Fulton County’s Big Creek WRF is being expanded to treat an increased volume and achieve more stringent effluent limits. The project is a $300 million investment into the facility and represents the largest capital project ever undertaken by the County. The County elected to utilize Progressive Design Build to provide a cost-effective expansion and ensure their involvement throughout the design process. The project procurement and construction has occurred during an unprecedented period in the construction industry with many market challenges including a pandemic, labor shortages, breakdown of the supply-chain, and unusual inflation. The use of the Progressive Design Build model has allowed the team to utilize design, procurement, and construction approaches that have successfully kept the project on schedule and within budget. This presentation will provide examples on how collaboration via PDB best practices can be used to successfully navigate a challenging construction market.
CONTENT EXPIRES: December 31, 2025
Fulton County’s Big Creek WRF is being expanded to treat an increased volume and achieve more stringent effluent limits. The project is a $300 million investment into the facility and represents the largest capital project ever undertaken by the County. The County elected to utilize Progressive Design Build to provide a cost-effective expansion and ensure their involvement throughout the design process. The project procurement and construction has occurred during an unprecedented period in the construction industry with many market challenges including a pandemic, labor shortages, breakdown of the supply-chain, and unusual inflation. The use of the Progressive Design Build model has allowed the team to utilize design, procurement, and construction approaches that have successfully kept the project on schedule and within budget. This presentation will provide examples on how collaboration via PDB best practices can be used to successfully navigate a challenging construction market.
-
Includes Credits Recorded On: 03/16/2023
CONTENT EXPIRES: December 31, 2025 The booming water/wastewater market is keeping design-builders very busy, leaving owners faced with the dilemma of how to sell their projects to the market. Equally applicable to owners and owners advisors, this session will explain how economic and technological factors are decreasing the number of bidders on projects and what owners can do about that. In todays market, it falls to owners to engage in early outreach so potential bidders know what projects are upcoming. Continual communication, in the form of updates, one-on-one confidential meetings, and written communication, will help design-build teams understand the project drivers and keep the project on their radar screens. It is in owners best interests to have a strategy and schedule for making key project decisions. Taking the time to select an appropriate delivery approach that aligns with project goals is key to a successful outcome. Sharing draft contracts with potential bidders and soliciting input on the terms will go a long way to developing a fair and balanced risk allocation. Design-builders will focus their efforts on projects they think they can win and successfully execute. Owners who make it easy for design-builders to assess those outcomes have the best shot of attracting qualified bidders.
CONTENT EXPIRES: December 31, 2025
The booming water/wastewater market is keeping design-builders very busy, leaving owners faced with the dilemma of how to sell their projects to the market. Equally applicable to owners and owners advisors, this session will explain how economic and technological factors are decreasing the number of bidders on projects and what owners can do about that. In todays market, it falls to owners to engage in early outreach so potential bidders know what projects are upcoming. Continual communication, in the form of updates, one-on-one confidential meetings, and written communication, will help design-build teams understand the project drivers and keep the project on their radar screens. It is in owners best interests to have a strategy and schedule for making key project decisions. Taking the time to select an appropriate delivery approach that aligns with project goals is key to a successful outcome. Sharing draft contracts with potential bidders and soliciting input on the terms will go a long way to developing a fair and balanced risk allocation. Design-builders will focus their efforts on projects they think they can win and successfully execute. Owners who make it easy for design-builders to assess those outcomes have the best shot of attracting qualified bidders.
-
Includes Credits Recorded On: 03/16/2023
CONTENT EXPIRES: December 31, 2025 Under the New York City Public Works Investment Act, the New York City Department of Environmental Protection (NYCDEP) received authorization to utilize the design-build project delivery method for capital projects. As this is a change from current practice, the NYCDEP embarked on DBIA training and prepared an implementation plan for delivering a portfolio of design build projects. The plan identified challenges, roles and responsibilities, and strategic approaches for implementation. The NYCDEP has progressed from the initial roadmap to a pilot program to deliver fixed price design build projects through a two-step procurement process. The NYCDEP is in the implementation phase which has included procuring owner advisor services, developing project selection criteria, shortlisting several candidate projects, developing new solicitation documents and review procedures, and identifying and coordinating with internal and external stakeholders. We will provide an overview of the program and discuss how the Agency is working through the challenges of transitioning into collaborative delivery method.
CONTENT EXPIRES: December 31, 2025
Under the New York City Public Works Investment Act, the New York City Department of Environmental Protection (NYCDEP) received authorization to utilize the design-build project delivery method for capital projects. As this is a change from current practice, the NYCDEP embarked on DBIA training and prepared an implementation plan for delivering a portfolio of design build projects. The plan identified challenges, roles and responsibilities, and strategic approaches for implementation. The NYCDEP has progressed from the initial roadmap to a pilot program to deliver fixed price design build projects through a two-step procurement process. The NYCDEP is in the implementation phase which has included procuring owner advisor services, developing project selection criteria, shortlisting several candidate projects, developing new solicitation documents and review procedures, and identifying and coordinating with internal and external stakeholders. We will provide an overview of the program and discuss how the Agency is working through the challenges of transitioning into collaborative delivery method.
-
Includes Credits Recorded On: 03/16/2023
CONTENT EXPIRES: December 31, 2025 Louisville MSD envisions a comprehensive Biosolids Processing Solution (BPS) at its Morris Forman facility for 130 ton/day (average) of biosolids. To MSD a comprehensive solution reduces the amount of biosolids for disposal, improves quality and moves towards holistic environmental management including renewable energy production. MSD enjoy many significant advantages including highly experienced operations and maintenance staff, a knowledgeable Owner's Advisor, a strong disadvantaged business community, commitment from executive leadership and a $97M WIFIA grant. However the ever changing landscape offered challenges to MSD as well including the global pandemic, rapidly escalating costs, emergency conditions to overcome challenges with existing biosolids processing equipment, a very tight site with no room for expansion and a fixed timeline for project completion. MSD has used the progressive design build delivery mechanism to engage a team to plot a path to the optimized comprehensive sustainable outcome. This presentation showcases MSD harnessing its staff, its advisors, the DB team, disadvantaged businesses, vendors and trade partners into a cohesive effective team. It covers 3D collaboration tools, coordination with ongoing projects, high value DBE engagement, routine value engineering solutions saving $40M+ from the project budget, and how planning for operations and financial return from the project was planned.
CONTENT EXPIRES: December 31, 2025
Louisville MSD envisions a comprehensive Biosolids Processing Solution (BPS) at its Morris Forman facility for 130 ton/day (average) of biosolids. To MSD a comprehensive solution reduces the amount of biosolids for disposal, improves quality and moves towards holistic environmental management including renewable energy production. MSD enjoy many significant advantages including highly experienced operations and maintenance staff, a knowledgeable Owner's Advisor, a strong disadvantaged business community, commitment from executive leadership and a $97M WIFIA grant. However the ever changing landscape offered challenges to MSD as well including the global pandemic, rapidly escalating costs, emergency conditions to overcome challenges with existing biosolids processing equipment, a very tight site with no room for expansion and a fixed timeline for project completion. MSD has used the progressive design build delivery mechanism to engage a team to plot a path to the optimized comprehensive sustainable outcome. This presentation showcases MSD harnessing its staff, its advisors, the DB team, disadvantaged businesses, vendors and trade partners into a cohesive effective team. It covers 3D collaboration tools, coordination with ongoing projects, high value DBE engagement, routine value engineering solutions saving $40M+ from the project budget, and how planning for operations and financial return from the project was planned.
-
Includes Credits Recorded On: 03/16/2023
CONTENT EXPIRES: December 31, 2025 This presentation will present the results of the Water Collaborative Delivery Association's current research into what makes collaborative delivery projects more successful than DBB. It extends the WCDA's 2021 research by examining specifically a series of the most important control points that govern how owners and practitioners start and finish projects to achieve success. It also examines the questions of readiness to undertake collaborative delivery and documents alternative approaches that owners and practitioners take (the most important control points across the project delivery life cycle to promote successful outcomes. This research is based on a series of focus groups of owners and separately, practitioners, as well as detailed project-specific interviews across owner organizations including executive management, procurement, finance, project management, and operations. A Beta version of the WCDA's new Readiness Self-Assessment Tool will be presented.
CONTENT EXPIRES: December 31, 2025
This presentation will present the results of the Water Collaborative Delivery Association's current research into what makes collaborative delivery projects more successful than DBB. It extends the WCDA's 2021 research by examining specifically a series of the most important control points that govern how owners and practitioners start and finish projects to achieve success. It also examines the questions of readiness to undertake collaborative delivery and documents alternative approaches that owners and practitioners take (the most important control points across the project delivery life cycle to promote successful outcomes. This research is based on a series of focus groups of owners and separately, practitioners, as well as detailed project-specific interviews across owner organizations including executive management, procurement, finance, project management, and operations. A Beta version of the WCDA's new Readiness Self-Assessment Tool will be presented.
-
Includes Credits Recorded On: 03/16/2023
CONTENT EXPIRES: December 31, 2025 Early cost certainty is a key benefit achieved by owners utilizing design-build delivery. Accurately pricing early design concepts requires skill and diligence under normal conditions, but unprecedented market volatility experienced since March 2020 has upped the ante. With unpredictability in pricing, material and equipment availability, and increasing labor costs, traditional approaches to predicting costs have become practically obsolete. Jacobs is currently delivering four design-build projects in different regions of the United States three progressive design-build delivery and one fixed-price design-build delivery. Two established pricing commitments in late 2020 and two established guaranteed maximum prices (GMPs) in 2021 and 2022, respectively. This presentation will compare approaches used for each project and highlight lessons learned that can be applied immediately, but also are worthy considerations for best practices in any market. These include: - Effective market engagement strategies to produce accurate cost estimates at various project stages - Cost escalation approaches to manage risk and attract market competition - Equipment and material procurement strategies to address supply chain shortages - Market input and validation of costs
CONTENT EXPIRES: December 31, 2025
Early cost certainty is a key benefit achieved by owners utilizing design-build delivery. Accurately pricing early design concepts requires skill and diligence under normal conditions, but unprecedented market volatility experienced since March 2020 has upped the ante. With unpredictability in pricing, material and equipment availability, and increasing labor costs, traditional approaches to predicting costs have become practically obsolete. Jacobs is currently delivering four design-build projects in different regions of the United States three progressive design-build delivery and one fixed-price design-build delivery. Two established pricing commitments in late 2020 and two established guaranteed maximum prices (GMPs) in 2021 and 2022, respectively. This presentation will compare approaches used for each project and highlight lessons learned that can be applied immediately, but also are worthy considerations for best practices in any market. These include: - Effective market engagement strategies to produce accurate cost estimates at various project stages - Cost escalation approaches to manage risk and attract market competition - Equipment and material procurement strategies to address supply chain shortages - Market input and validation of costs
-
Includes Credits Recorded On: 03/16/2023
CONTENT EXPIRES: December 31, 2025 The Silicon Valley Clean Water Gravity Pipeline Tunnel Project is a 3.2 mile long, 11 ft. ID sewer pipeline project excavated by a 16 ft. diameter EPB TBM in Redwood City, California. A key technical challenge was low ground cover under shallow structures and roadways in a challenging geological formation that commonly generates surface settlements. The sensitive context of this project led the owner, SVCW, in 2017 to select a progressive design and build delivery method—a first for North America. As the project is now complete, the points of view of all parties involved in the project have been captured and reflected upon. This paper shares the perspectives from the Owner, Construction Manager, Engineer of Record, technical advisors and Contractor to discuss the merits of the PDB delivery method while retracing the evolution of the procurement, the design, the project approach, the value engineering exercises, the technical development alongside the risk assessments, the team building, and the construction from the beginning to final completion.
CONTENT EXPIRES: December 31, 2025
The Silicon Valley Clean Water Gravity Pipeline Tunnel Project is a 3.2 mile long, 11 ft. ID sewer pipeline project excavated by a 16 ft. diameter EPB TBM in Redwood City, California. A key technical challenge was low ground cover under shallow structures and roadways in a challenging geological formation that commonly generates surface settlements. The sensitive context of this project led the owner, SVCW, in 2017 to select a progressive design and build delivery method—a first for North America. As the project is now complete, the points of view of all parties involved in the project have been captured and reflected upon. This paper shares the perspectives from the Owner, Construction Manager, Engineer of Record, technical advisors and Contractor to discuss the merits of the PDB delivery method while retracing the evolution of the procurement, the design, the project approach, the value engineering exercises, the technical development alongside the risk assessments, the team building, and the construction from the beginning to final completion.
-
Includes Credits Recorded On: 03/16/2023
CONTENT EXPIRES: December 31, 2025 The San Antonio River Authority (River Authority) used Progressive Design-Build (PDB) delivery for the Salitrillo Wastewater Treatment Plant (WWTP) Expansion project, which expanded the WWTP from a capacity of 5.83 million gallons per day (MGD) to 7.33 MGD. This delivery method was new for the River Authority, and it quickly became an effective but challenging way to manage schedule and cost in a new virtual environment. The RFQ was issued 01/08/22, after which the qualified design-build teams were shortlisted. An RFP was then issued on 03/16/20, the same day San Antonios mayor issued an emergency declaration urging the public to avoid gatherings of ten or more people. Along with the new challenge of collaborating in a virtual environment, there were issues during construction with cost escalation and material delays that tested the flexibility and benefits of PDB. This presentation will discuss the following from an owners and design-builders perspective: The procurement process and associated challenges and solutions Best contracting practices in a volatile construction market Project management lessons learned Managing constant fluctuations in raw material and equipment costs during pre-construction and construction phase Pros and cons of using PDB, and recommendations for using this method
CONTENT EXPIRES: December 31, 2025
The San Antonio River Authority (River Authority) used Progressive Design-Build (PDB) delivery for the Salitrillo Wastewater Treatment Plant (WWTP) Expansion project, which expanded the WWTP from a capacity of 5.83 million gallons per day (MGD) to 7.33 MGD. This delivery method was new for the River Authority, and it quickly became an effective but challenging way to manage schedule and cost in a new virtual environment. The RFQ was issued 01/08/22, after which the qualified design-build teams were shortlisted. An RFP was then issued on 03/16/20, the same day San Antonios mayor issued an emergency declaration urging the public to avoid gatherings of ten or more people. Along with the new challenge of collaborating in a virtual environment, there were issues during construction with cost escalation and material delays that tested the flexibility and benefits of PDB. This presentation will discuss the following from an owners and design-builders perspective: The procurement process and associated challenges and solutions Best contracting practices in a volatile construction market Project management lessons learned Managing constant fluctuations in raw material and equipment costs during pre-construction and construction phase Pros and cons of using PDB, and recommendations for using this method
-
Includes Credits Recorded On: 03/16/2023
CONTENT EXPIRES: December 31, 2025 This session will review the delivery method for the Northeast Water Purification Plant Expansion in Houston, TX. The presentation will focus on the importance of the schedule and planning for Early Work Package delivery. We will review the decision making for the scope of work for these packages along with the funding process. The presenters will also present how these packages have been incorporated, closed out, and assisted with the schedule. The audience will also get a lessons learned from the Owners perspective.
CONTENT EXPIRES: December 31, 2025
This session will review the delivery method for the Northeast Water Purification Plant Expansion in Houston, TX. The presentation will focus on the importance of the schedule and planning for Early Work Package delivery. We will review the decision making for the scope of work for these packages along with the funding process. The presenters will also present how these packages have been incorporated, closed out, and assisted with the schedule. The audience will also get a lessons learned from the Owners perspective.